In the world of food manufacturing, the paramount concern is the safety and quality of the products that reach consumers. With the increasing demand for food safety, manufacturers continuously seek advanced technologies to ensure their products are free from contaminants. Among these technologies, metal detectors are pivotal in maintaining high food safety standards in manufacturing.
This article delves into how metal detectors can enhance food safety in manufacturing.
The Importance Of Metal Detectors In Food Safety
Metal contamination can occur at any stage of the food production process, from the initial raw material handling to the final packaging. Contamination sources are diverse, including machinery wear and tear, processing equipment, and accidental introduction during handling. Metal particles in food products pose a serious health risk to consumers, leading to costly recalls, legal issues, and damage to a brand’s reputation. This is where metal detectors come into play.
Metal detectors are designed to detect and reject any metallic contaminants, whether ferrous, non-ferrous, or stainless steel, which might be present in food products. Integrating these devices into production lines helps identify and eliminate potential hazards, thus safeguarding consumer health and upholding the manufacturer’s reputation.
Hence, for those involved in food production and seeking to enhance their safety protocols, food manufacturers may visit here or check reputable resources to gain comprehensive insights into the latest advancements in metal detection and check weigher systems, which are integral to ensuring product integrity.
Ways Metal Detectors Enhance Food Safety
After understanding the importance of metal detectors, the next step is to get familiar with ways these devices can improve food safety in manufacturing. These may include:
They Offer Advanced Detection Capabilities
Modern metal detectors in the food manufacturing sector are equipped with cutting-edge technology, offering high sensitivity to detect minuscule metallic particles that could compromise food safety. These devices utilize the principle of electromagnetic induction to generate a high-frequency magnetic field.
As food products pass through this field, any metallic contaminants disrupt the field, instantly triggering an alert in the detector. This advanced detection capability is vital for several reasons:
- Precision: Metal detectors ensure the identification of extremely small metal fragments that manual inspections might miss.
- Versatility: They can detect various metals, including ferrous, non-ferrous, and stainless steel.
- Speed: Metal detectors’ rapid detection allows for real-time quality control without slowing down production lines.
- Adaptability: Their settings can be adjusted to cater to different product types and packaging materials, enhancing detection accuracy.
This high sensitivity and adaptability ensure that metal detectors are essential in maintaining the integrity and safety of food products.
They Ensure Compliance with Food Safety Standards
Implementing advanced metal detection systems in food manufacturing is a vital compliance strategy. Regulatory agencies across the globe have set rigorous food safety standards to protect consumers. Metal detectors play a crucial role in this framework by:
- Detecting Contaminants: Identifying and removing metallic particles is crucial to prevent potential health hazards.
- Meeting Standards: Aligning with food safety protocols is required by entities like the Food and Drug Administration (FDA).
- Documenting Safety: Providing a record of due diligence and compliance efforts is essential for audits.
- Building Trust: Assuring consumers of the safety and quality of their food products is critical for ensuring compliance with certain food safety measures.
By integrating metal detectors and chart recorders for fluid processing, manufacturers protect consumer health and contribute to more efficient and sustainable operations, ensuring that resources are used judiciously, and waste is minimized.
They Integrate with Production Lines Seamlessly
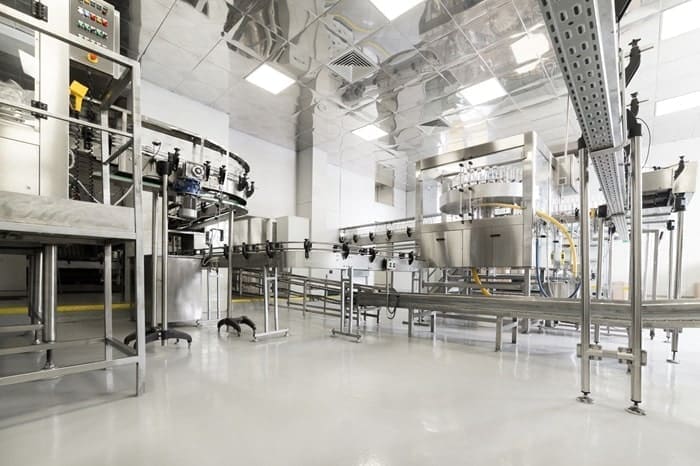
The seamless integration of metal detectors into food production lines is a testament to their versatility and adaptability. Manufacturers can incorporate these sophisticated devices at multiple points in the manufacturing process, ensuring thorough inspection and food safety. Key integration points include:
- Raw Material Inspection: Metal detectors can screen incoming materials to prevent contamination at the source.
- Pre-Packaging Check: They ensure products are free of metal before final packaging
- Post-Packaging Inspection: Metal detectors can verify the integrity of the final packaged product, including the packaging material itself.
- In Line with Other Systems: They can work in tandem with checkweighers and X-ray systems for a comprehensive inspection approach.
Strategic placement allows customization of the detection system to meet unique operational needs, enhancing safety and efficiency.
They Help Reduce Product Waste
Product waste is minimized when food manufacturers run metal detectors. Only the contaminated products are removed from the production line.
This targeted approach provides key benefits:
- Minimized Recalls: By detecting and removing contaminated items early, the likelihood of extensive recalls that waste large quantities of food is significantly reduced.
- Preservation of Safe Products: Accurate detection means that safe, non-contaminated products aren’t discarded unnecessarily, conserving valuable resources.
- Operational Efficiency: Streamlining the detection process reduces downtime and material waste, enhancing overall productivity.
- Sustainability: Less waste contributes to more sustainable production practices, aligning with environmental goals.
Metal detectors help manufacturers improve operations and safeguard their clients’ health. They ensure effective resource utilization and reduce waste.
They Ensure Continuous Improvement and Innovation
Metal detection technology is marked by constant evolution and innovation, ensuring that
food manufacturing processes remain at the forefront of safety and efficiency.
This ongoing advancement is driven by the following:
- Enhanced Sensitivity: Improvements in technology allow for the detection of even finer metal particles, reducing the risk of contamination.
- Increased Speed: Newer models can scan products faster without compromising accuracy, keeping pace with fast-moving production lines.
- Greater Reliability: Continuous enhancements in design and software lead to more dependable systems that reduce false positives and ensure consistent performance.
- Adaptability to New Challenges: As food manufacturing processes become more complex, metal detection technology evolves to meet new safety and regulatory demands.
This commitment to research and development ensures that the food manufacturing industry is equipped with cutting-edge tools, maintaining the highest product safety and quality standards.
They Help Enhance Consumer Confidence
Implementing metal detectors in food manufacturing can significantly boost consumer confidence by ensuring that products are rigorously screened for safety. This reassurance is pivotal in building trust and loyalty towards brands for several reasons:
- Guaranteed Safety: Metal detectors assure that food items are free from harmful metallic contaminants.
- Quality Assurance: They offer a commitment to high-quality standards in production.
- Brand Trust: Metal detectors provide confidence in brands that invest in advanced safety technologies.
- Transparency: They ensure openness about safety protocols, which resonates with informed consumers.
By prioritizing the safety and quality of their products through metal detectors, manufacturers can cultivate a strong bond with consumers, who value the peace of mind that comes with consuming safe and well-inspected products.
Conclusion
Metal detectors are indispensable in the modern food manufacturing industry, serving as a critical line of defense against metallic contaminants. By considering the information mentioned above, manufacturers can ensure compliance with stringent food safety standards, protect consumers, maintain brand integrity, and enhance operational efficiency.
As technology advances, the capabilities of metal detection systems will continue to improve, further bolstering the industry’s commitment to producing safe, high-quality food products.